In today’s fast-paced and ever-evolving industrial landscape, it’s crucial for us to stay ahead of the curve. That’s why we’re diving headfirst into the exciting world of Artificial Intelligence (AI) and its remarkable applications in the manufacturing industry.
Picture this: an intelligent system that can predict and prevent future problems, generate innovative ideas, and uncover deep insights from vast amounts of data. That’s the power of AI in manufacturing! It’s not just about automating repetitive tasks; AI has the potential to revolutionize how we approach production, operations, and quality control processes.
In this article, I’ll be your trusty guide to explore the incredible possibilities that AI brings to our manufacturing realm. I’ll take you on a journey through real-world examples, showcasing how AI is already making a significant impact in the industry. But we won’t stop there! I’ll also highlight the untapped potential of AI and what lies ahead for us as we embrace this transformative technology.
Understanding AI in Manufacturing
In this section, we’ll unravel the essence of AI in the context of the manufacturing industry. If you’re new to the concept, don’t worry; I’ll break it down for you.
Artificial Intelligence, or AI, refers to the simulation of human intelligence in machines programmed to perform tasks that typically require human cognitive abilities. In the realm of manufacturing, AI empowers us to go beyond traditional automation and unlocks intelligent decision-making. It’s like having a smart assistant that can analyze vast amounts of data, identify patterns, and provide valuable insights to optimize various processes, all in no time.
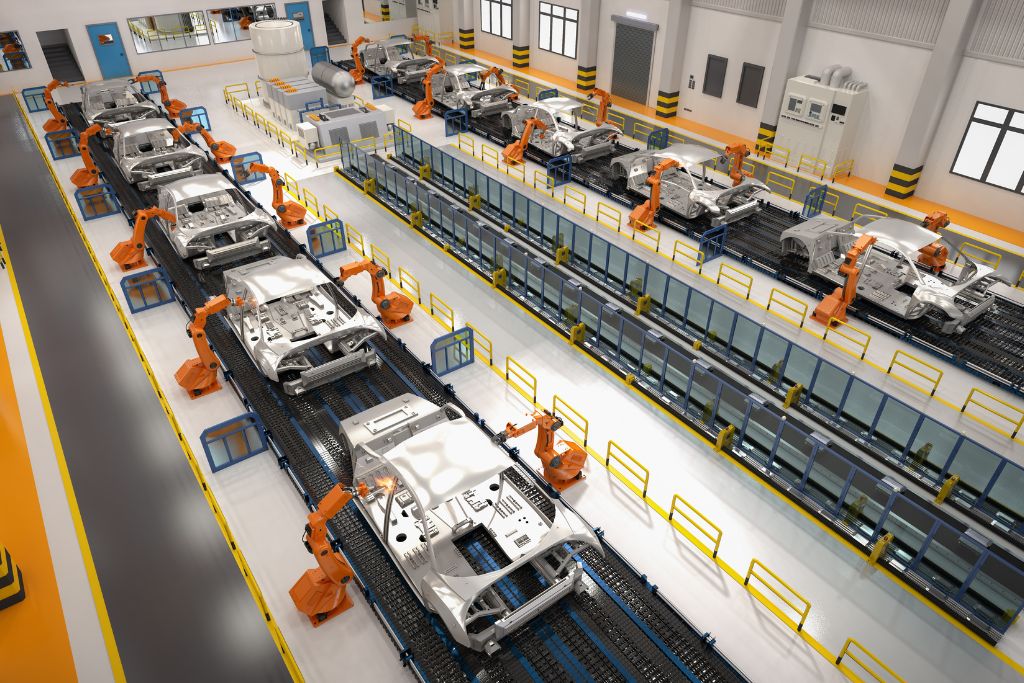
AI’s potential in manufacturing extends far and wide. From streamlining production lines to enhancing quality control, AI can revolutionize the way we operate. Picture AI-powered robots collaborating seamlessly with human workers, analyzing data in real-time to detect anomalies and prevent potential issues. Think of AI as your strategic partner, driving innovation and efficiency across multiple sectors of manufacturing.
In the world of AI, data is the lifeblood that fuels innovation. The manufacturing industry generates a massive amount of data every day, from sensor readings on machinery to production logs and customer feedback. AI thrives on this data, using it to learn, adapt, and optimize processes. The more data AI can access, the more accurate and insightful its decisions become.
AI Applications in Manufacturing
Here are some of the most common applications of AI in the manufacturing industry. From automation to predictive maintenance and repair, the manufacturing industry can get a significant boost from AI and machine learning.
Automation in Manufacturing
In the manufacturing world, AI is a powerful force driving automation to new heights. By taking on repetitive tasks and optimizing operations, AI enables manufacturers to achieve unprecedented levels of efficiency.
With AI at the helm, routine tasks that once demanded significant human effort are now seamlessly automated. From assembly lines to material handling, AI-powered robots work side by side with human operators, boosting productivity and reducing errors.
Here are some real-world examples of AI-driven automation in manufacturing.
- Quality Inspection: AI-based machine vision systems can analyze products with precision, identifying defects and ensuring only the highest-quality items reach customers.
- Predictive Maintenance: AI algorithms can also monitor equipment performance, predicting maintenance needs before breakdowns occur, thus reducing downtime and avoiding costly repairs.
- Demand Forecasting: AI’s data-driven analysis allows manufacturers to anticipate fluctuations in demand, optimizing production schedules and inventory management.
- Supply Chain Management: AI also optimizes logistics and supply chain processes by predicting demand patterns, reducing transportation costs, and enhancing inventory control.
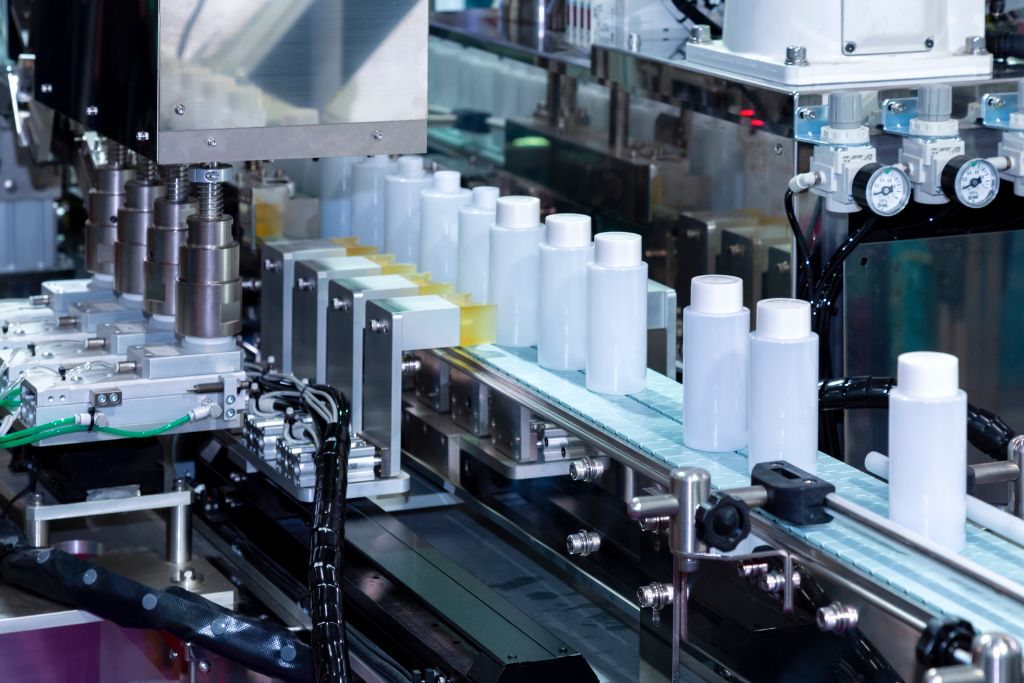
Predictive Maintenance with AI
Predictive maintenance is a game-changer for the manufacturing industry, offering a proactive approach to equipment upkeep and reliability. By leveraging AI algorithms and data analytics, manufacturers can predict potential equipment failures, optimize maintenance schedules, and reduce unplanned downtime.
What is Predictive Maintenance?
Predictive maintenance uses AI and machine learning algorithms to analyze real-time data from sensors and machineries. In traditional maintenance practices, equipment is often serviced based on fixed schedules or when it breaks down unexpectedly.
By monitoring equipment health, AI can detect early signs of wear and identify anomalies, providing a warning before a failure occurs. This enables manufacturers to take preventive measures and conduct maintenance at the most opportune times, avoiding costly disruptions.
AI Algorithms for Equipment Failure Prediction
AI algorithms excel at processing vast amounts of data, including temperature, vibration, pressure, and other sensor readings. By analyzing historical and real-time data, AI can identify patterns and trends associated with equipment failures. This enables predictive models to continuously learn and adapt, becoming more accurate over time.
Through predictive maintenance, manufacturers can anticipate issues such as component wear, fatigue, or lubrication problems. Armed with this foresight, maintenance teams can take proactive actions, saving costs on unnecessary repairs and maximizing equipment lifespan.
Case Studies of Successful Predictive Maintenance Implementations
Aircraft Engine Maintenance: Bell Flight, an aircraft engine manufacturer, utilized AI-driven predictive maintenance to monitor engine health in real-time. By analyzing sensor data during flights, the AI system predicted impending faults, prompting the maintenance team to conduct targeted inspections and replacements.
“One powerful benefit illustrated by the exercise was how predicting the failure of a relatively low-cost part can avoid the need to replace an entire system—such as an engine—saving well over US$12 million.”
Peter Shultz, Bell Flight
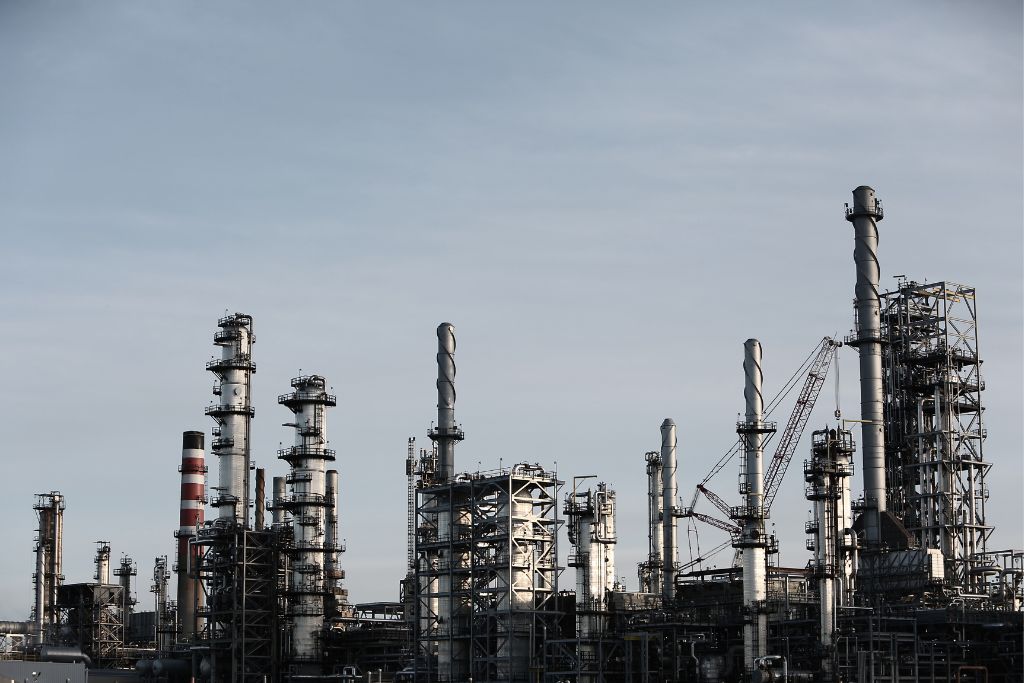
Smart Manufacturing Plant: Smart manufacturing plants like ABB and General Electric implement AI-based predictive maintenance on their production machinery. The AI system detects subtle changes in equipment performance, enabling timely maintenance interventions. As a result, the plants reduce their downtime, leading to increased productivity and cost savings.
Energy Sector Optimization: In the energy sector, predictive maintenance has revolutionized maintenance practices for wind turbines. AI algorithms analyze turbine data, predicting potential faults and allowing operators to schedule maintenance during optimal weather conditions. This strategy has significantly decreased maintenance costs and increased turbine uptime.
Quality Control and Defect Detection
Quality control is of paramount importance in manufacturing, and AI has emerged as a powerful ally in ensuring top-notch product quality. Let’s explore how AI transforms quality control processes and revolutionizes defect detection.
Enhancing Quality Control Processes with AI
AI brings a data-driven approach to quality control, enabling manufacturers to identify and rectify defects swiftly. By analyzing data from various stages of production, AI can pinpoint deviations from standard quality parameters and alert operators in real-time. This proactive intervention ensures that potential issues are addressed promptly, minimizing the risk of producing faulty goods.
Moreover, AI-powered visual inspection systems excel at detecting defects that might be challenging for the human eye to spot. This precision improves product consistency and customer satisfaction, fostering brand loyalty and market reputation.
AI-Driven Defect Detection Techniques
AI employs advanced computer vision algorithms to analyze visual data and detect defects effectively. Convolutional Neural Networks (CNNs) and Deep Learning models enable AI systems to recognize patterns and anomalies in product images with exceptional accuracy.
The advantages of AI-driven defect detection lie in its speed, reliability, and scalability. It can also eliminate the potential for human error, detect multiple flaws at the same time, go above and beyond surface-level detection, and more. AI-powered inspection systems can process a vast number of items per minute, ensuring that products meet the highest quality standards before reaching consumers.
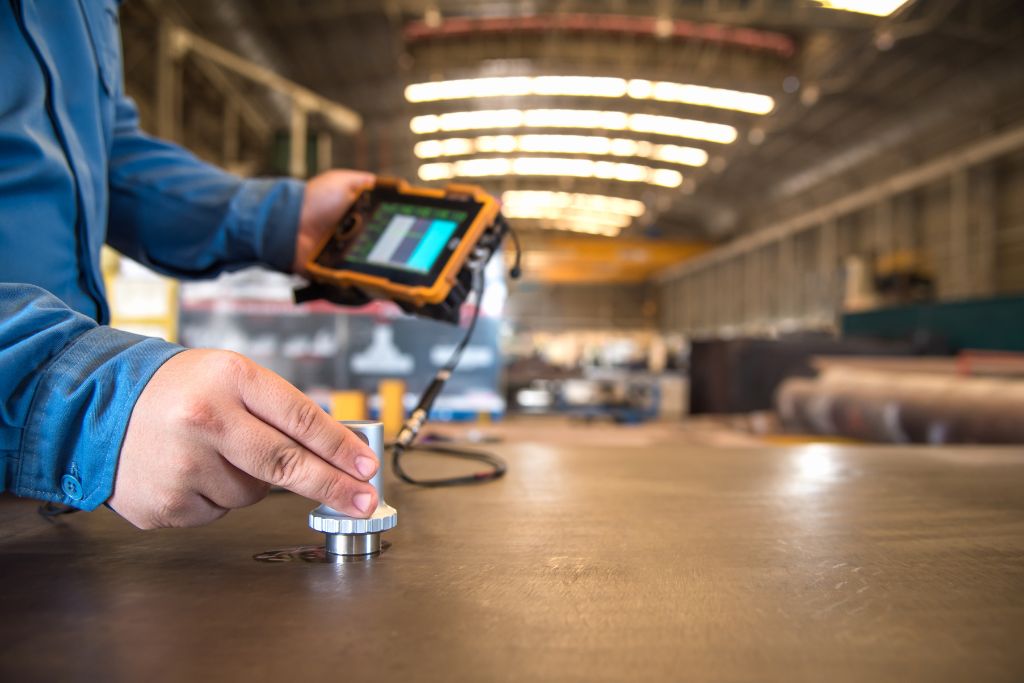
Use Cases of AI-Based Quality Control in Manufacturing
- Automotive Industry: Automotive manufacturers rely on AI-driven quality control to inspect critical components such as engine parts and safety-critical systems. AI-powered vision systems can detect micro-defects, dimensional variations, and pseudo-defects, guaranteeing the safety and reliability of vehicles.
- Electronics Manufacturing: In electronics production, AI-based quality control ensures the integrity of microelectronics. Defect detection algorithms help identify flaws in circuitry, soldering, and surface finish, contributing to the flawless functionality of electronic devices.
- Pharmaceutical Sector: AI is increasingly employed in pharmaceutical quality control to assess drug dosage precision and detect impurities. These AI-powered systems play a vital role in upholding the pharmaceutical industry’s stringent regulatory standards.
Forecasting Raw Material Prices
The ability to forecast raw material prices accurately is crucial for manufacturers’ strategic decision-making. AI’s analytical capabilities empower businesses to analyze market data and predict raw material price fluctuations with precision.
AI’s Market Data Analysis for Price Forecasting
AI algorithms excel at analyzing vast and diverse datasets, including historical market prices, supply chain trends, geopolitical factors, and global economic indicators. By identifying patterns and correlations within this data, AI models can generate accurate forecasts of raw material prices.
AI’s learning capacity allows it to adapt to changing market conditions, making its predictions more reliable over time. Manufacturers can use these forecasts to anticipate potential price fluctuations and strategize their procurement and inventory management accordingly.
Strategic Procurement Decisions
Accurate raw material price forecasts empower manufacturers to make informed procurement decisions. When AI predicts a potential price increase for a specific raw material, manufacturers can secure bulk purchases at current rates, avoiding the impact of rising costs.
Conversely, when AI indicates a likely price decrease, manufacturers can delay procurement and take advantage of cost savings. This foresight allows businesses to optimize their spending and maintain a competitive edge in the market.
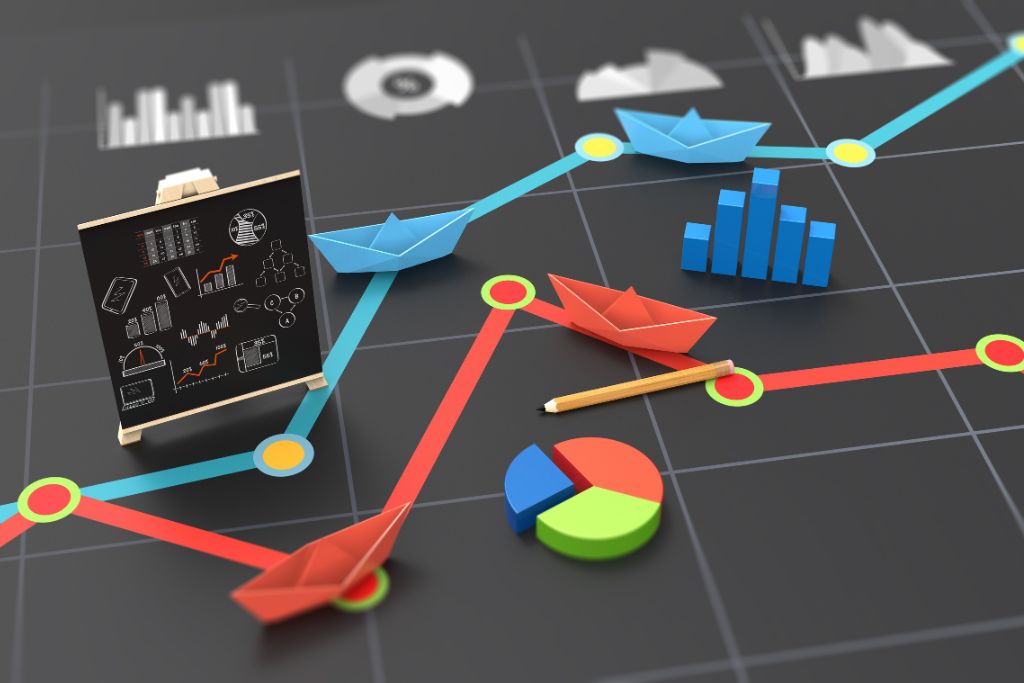
Benefits of AI in Manufacturing
Artificial Intelligence (AI) is reshaping the manufacturing landscape, bringing forth a myriad of benefits that optimize processes and elevate overall performance. Let’s delve into the significant advantages of integrating AI in manufacturing operations.
Increased Efficiency and Productivity
AI’s ability to automate repetitive tasks and streamline operations significantly boosts production efficiency. By delegating mundane activities to AI-powered systems, human workers can focus on more strategic and creative aspects of manufacturing. This newfound efficiency leads to accelerated production cycles and improved output.
Manufacturers that embrace AI-driven automation witness reduced lead times due to faster and more precise processes. For instance, AI-powered robots on assembly lines work seamlessly with human operators, resulting in faster production cycles. This increased efficiency leads to higher output and greater overall productivity.
Cost Savings and Waste Reduction
AI’s predictive maintenance capabilities revolutionize maintenance practices, enabling manufacturers to conduct timely interventions and prevent costly breakdowns. By addressing maintenance needs proactively, AI-driven systems minimize downtime, reduce maintenance costs, and extend the lifespan of equipment.
Furthermore, AI optimizes manufacturing processes by analyzing data and identifying areas of improvement. With AI’s insights, manufacturers can enhance material usage and reduce wastage during production. This eco-friendly approach not only saves costs but also aligns with sustainable manufacturing practices.
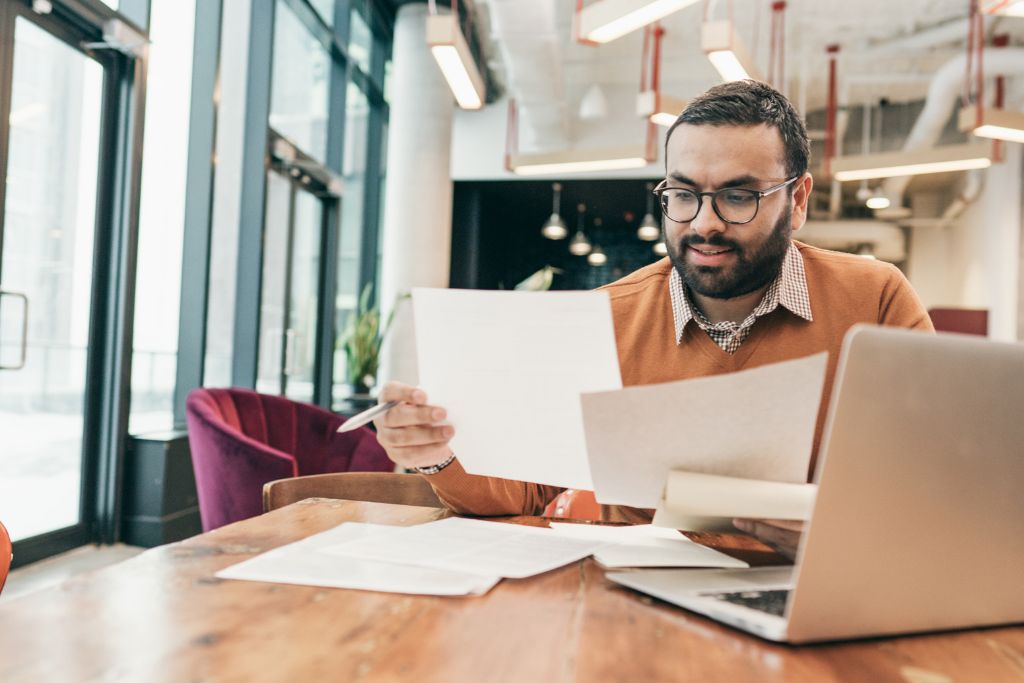
Enhanced Product Quality
AI’s precision in inspecting and analyzing product quality ensures consistency across batches. AI-powered vision systems identify even the slightest defects or variations, guaranteeing that all products meet stringent quality standards. Enhanced product consistency enhances customer satisfaction and builds trust in the brand.
AI-driven defect detection minimizes the production of defective products. By spotting anomalies in real-time, AI ensures that faulty items are detected and removed from the production line before they reach consumers. This results in cost savings and protects the brand’s reputation.
Improved Decision Making
AI’s data analysis capabilities generate valuable insights from vast datasets. By processing and interpreting data, AI aids decision-makers in understanding complex patterns and trends. This data-driven approach enables informed and strategic decision-making at various levels of the manufacturing process.
In today’s fast-paced manufacturing environment, real-time data analysis is invaluable. AI processes data instantaneously, allowing manufacturers to respond promptly to changing conditions. By making decisions based on up-to-date information, manufacturers can optimize efficiency and adapt to dynamic market demands effectively.
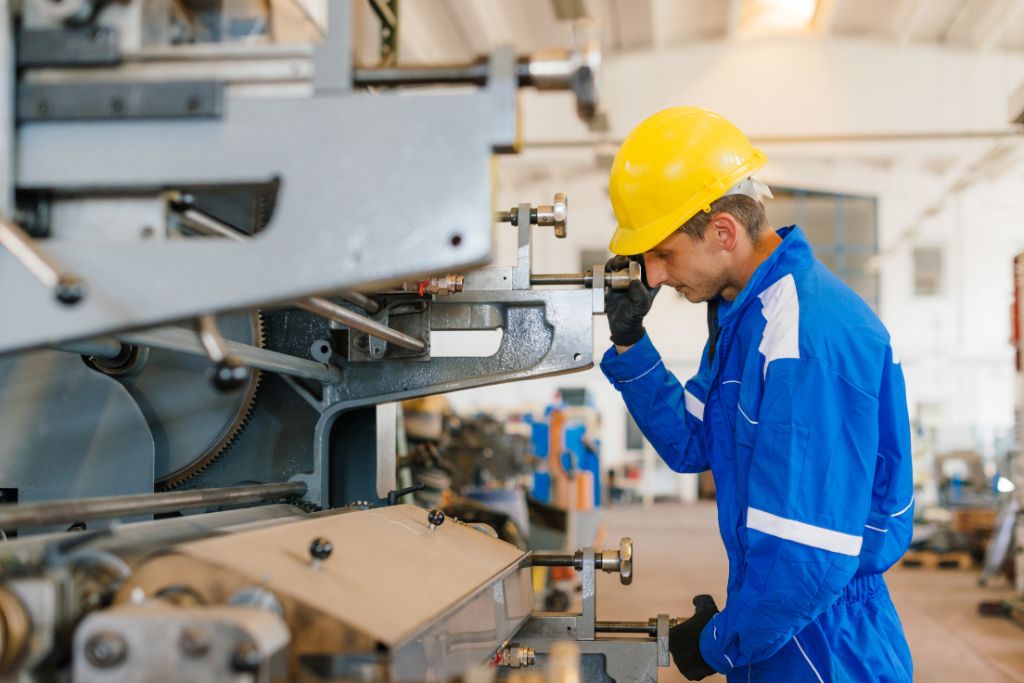
Conclusion
In this journey through the realm of AI in manufacturing, we’ve uncovered the transformative potential of this cutting-edge technology. Let’s recap the key points discussed and reflect on the profound impact AI can have on shaping the future of manufacturing.
Throughout the article, we’ve explored various applications of AI in manufacturing, ranging from automation and predictive maintenance to quality control and decision-making. AI-driven automation streamlines operations, reduces lead times, and enhances overall productivity.
Predictive maintenance ensures minimal downtime and cost savings by proactively addressing equipment needs. AI-powered quality control guarantees product consistency and reduces defective items. The data-driven insights provided by AI facilitate better decision-making, empowering manufacturers with real-time analytics for informed choices.
AI is not just a buzzword; it is a catalyst for innovation and progress in the manufacturing industry. As we embrace AI technologies, we unlock unprecedented opportunities for growth, efficiency, and enhanced customer experiences. AI’s ability to analyze vast datasets, predict outcomes, and optimize processes can drive manufacturing to new heights of excellence.
By harnessing AI’s potential, manufacturers can stay ahead of the competition, adapt to dynamic market demands, and make strategic decisions with confidence. Embracing AI is not just a choice; it’s a necessity for manufacturers who seek to thrive in an increasingly digital and data-centric era.
As the future unfolds, AI will continue to redefine manufacturing, and those who embrace it will lead the charge towards a more efficient, innovative, and prosperous tomorrow.